The process began with operational meetings to identify the lifting points and confirm that they were properly installed. While the mining cells were being built, we worked with plans until we could validate everything in the field and adjust the details.
The maneuvering and loading area was also evaluated, and with the final measurements, it was determined what would be packed, how to do it, and which equipment to use. Based on that, the economic proposal was created, and the suitable transportation units and shipping containers were selected.
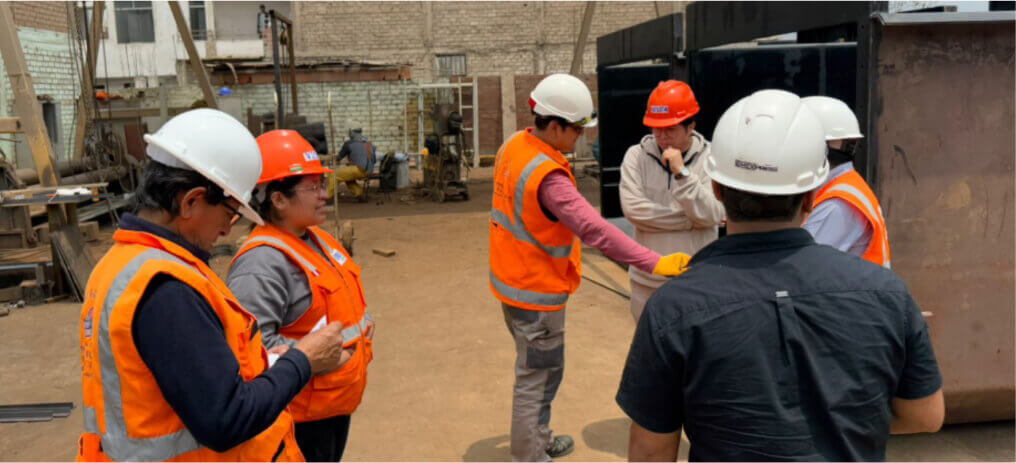